Common problems of checkweighers in assembly line work
2024-07-18
As a key equipment for quality control, the accuracy and stability of the checkweigher are directly related to the qualified rate of products and the economic benefits of enterprises. However, in actual applications,
checkweighers often encounter some problems in assembly line work, which will not only affect the production progress, but also may cause losses to enterprises.
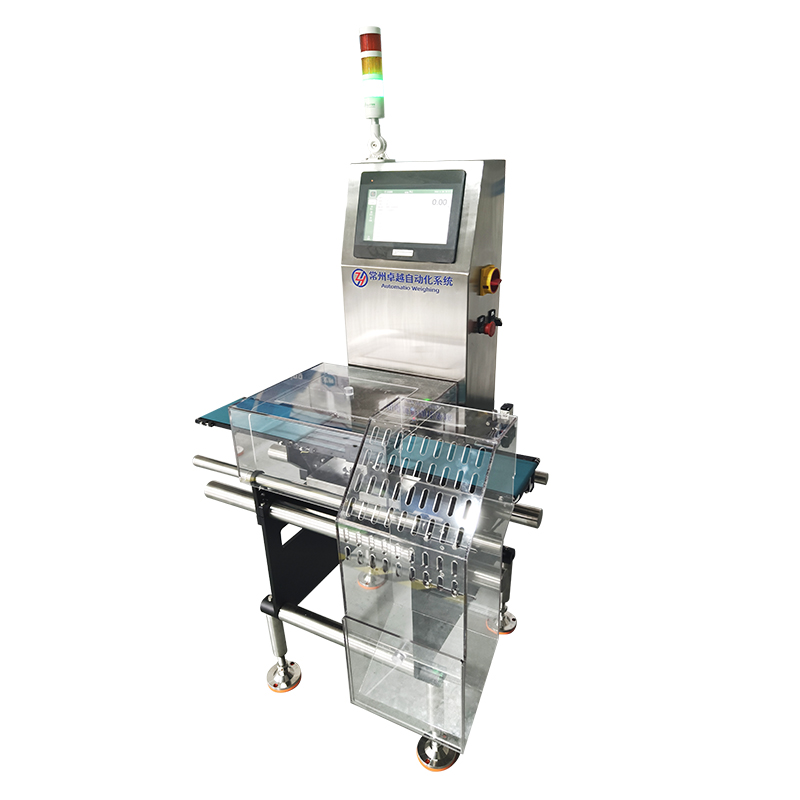
1. Accuracy problem
The accuracy of the checkweigher is one of the important indicators to measure its performance. However, in actual applications, due to the influence of various factors, the accuracy of the checkweigher often deviates. For example, changes in ambient temperature and humidity, equipment aging, vibration interference, etc. may all lead to a decrease in the accuracy of the checkweigher. When the accuracy of the checkweigher is insufficient, misjudgment, missed inspection, etc. may occur, which seriously affects the quality of the product.
Solution: First, the checkweigher should be calibrated and maintained regularly to ensure that its accuracy meets the production requirements. Secondly, when selecting a checkweigher, its accuracy level and stability should be fully considered, and equipment suitable for its own production needs should be selected. In addition, vibration interference can be reduced and the stability of the checkweigher can be improved by adding shock-absorbing devices and adjusting the equipment layout.
2. Speed problem
In assembly line operation, the detection speed of the checkweigher directly determines the production efficiency. However, some
checkweighers have limitations in detection speed and cannot meet the needs of high-speed production lines. When the detection speed of the checkweigher is too slow, it may cause problems such as production line congestion and product backlog, affecting production progress.
Solution: First, a checkweigher with high-speed detection capability should be selected to meet the actual needs of the production line. Secondly, the detection speed can be improved by optimizing the software algorithm of the checkweigher and increasing the processing speed of the equipment. In addition, technical means such as parallel detection and distributed processing can be used to further improve the detection efficiency of the checkweigher.
3. Adaptability problem
With the continuous development of production technology and the increasing number of product types, assembly line operations have higher and higher requirements for the adaptability of checkweighers. However, some checkweighers have deficiencies in adaptability and cannot adapt to the detection needs of products of different specifications and shapes. When the checkweigher is not adaptable enough, problems such as false detection and missed detection may occur, affecting product quality and production efficiency.
Solution: First, we should choose a checkweigher with wide adaptability, which can meet the inspection needs of products of different specifications and shapes. Secondly, we can improve its adaptability by adjusting the sensor position of the checkweigher and replacing conveyor belts of different specifications. In addition, we can also use technical means such as intelligent recognition and automatic adjustment to enable the checkweigher to automatically identify product specifications and shapes and automatically adjust the inspection parameters.
4. Reliability issues
In assembly line operations, the reliability of the checkweigher is one of the important factors to ensure smooth production. However, some checkweighers often fail or have abnormal conditions during operation, resulting in production interruptions or product quality problems. When the reliability of the checkweigher is insufficient, it will cause losses to the company.
Solution: First, we should choose a checkweigher with high reliability to ensure that it can work stably and reliably during operation. Secondly, we should regularly maintain and service the checkweigher to promptly detect and deal with potential problems. In addition, we can also use technical means such as redundant design and backup system to improve the fault tolerance and reliability of the checkweigher.