The main differences between checkweighers and static weighers
2024-09-30
Before the use of
checkweighers, product weight was usually measured using a static scale, where the product was manually placed on the table of the static scale for weighing, and then manually sorted or rejected based on the measured weight. The main differences between manual weighing with a static scale and automatic weighing with a checkweigher are:
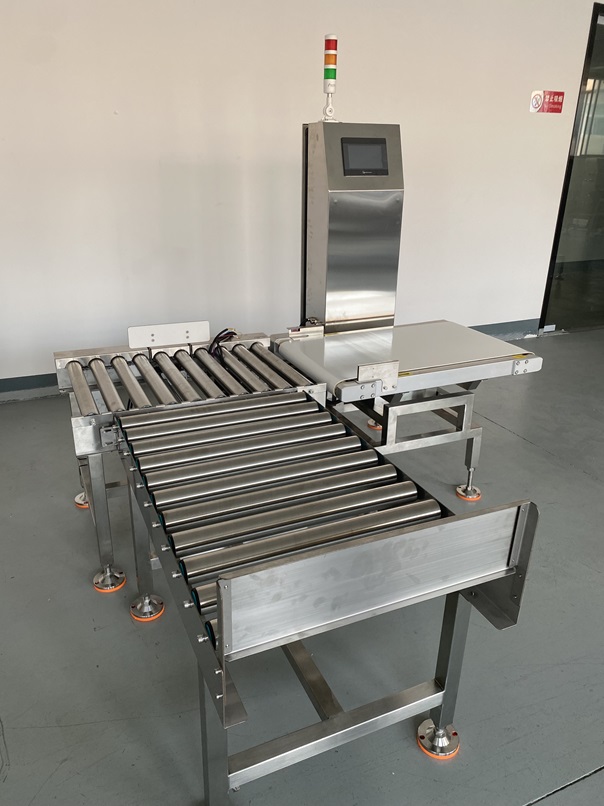
1) Static scales measure the static weight of the product, while most
checkweighers measure the dynamic weight of the product in motion (even if there are very few checkweighers that use a relatively static weighing process, the relative static time is very short).
2) Static scale weighing is a manual operation, requiring manual weighing of the product on the carrier, and then removing the product to prepare for the next product weighing. Checkweigher weighing is fully automatic, and the product is weighed as it passes along the production line, without manual intervention or dedicated operators.
3) Static scales are manual operations for product sorting or rejection of unqualified products, which are inevitably prone to errors. The corresponding operation of the checkweigher is automatically performed by the rejection device controlled by the weighing display, with high accuracy.
4) The working efficiency of static scales is very low, so for large quantities of products, a certain proportion of samples (such as 1% or less) are usually taken manually for on-site random inspection and weighing, while the checkweigher automatically checks the proportion of outgoing products at 100%.
5) Static scale weighing has higher accuracy and better repeatability, while the accuracy and repeatability of the checkweigher are slightly worse.
6) If static scale weighing needs to record data, manual handwriting is required. The checkweigher can automatically record data and classify it to achieve big data management, and can also realize feedback control of the filling amount of the filling machine through product weight data.
Among the above differences, the 100% product inspection of the dynamic checkweigher is very critical to ensure product quality. For example, if a production line has a product throughput of 100 pieces per minute, if the static scale manually samples 30 pieces per hour, the sampling rate is only: 30÷(100X60)=0.5%. Such a low sampling rate has little significance for the statistical analysis of the results, and it is difficult to guarantee the quality of the remaining 99.5% of the goods. (Excerpt from "Checkweigher")